Abstract
Hand-held electrical tools manufacturers are obligated to declare the level of vibrations generated by their tools. This level is estimated in accordance to certain standards. It is well known that working conditions vary much from the normative conditions. Apart from that, many factors can influence the level of vibrations. It has been hypothesized, that the drill’s bit diameter influences the tool’s handle level of vibrations. An awareness of vibration-causing factors is important not only for a user, but also for tool constructors and designers of personal safety means. The results of studies conducted in order to verify the hypothesis are presented in this paper.
1. Introduction
Right now there is a rich choice of different hand-held electrical tools available. The power level of these tools varies from a few dozens of watts to 2 kW. A significant part of these tools despite being approved and marketable and having a proper electro-energetic protection do not fulfil all the safety requirements concerning vibrations and noise emission [1]. Unfortunately, most impact drills create vibrations above the permissible level of intensity – 11.2 m/s2 [2].
The values of accelerations of the emitted vibrations and noise declared by their manufacturers are valid for the conditions within certain standards [3] and may differ much from the working conditions. The subject of the factors determining the level of vibrations has been brought up in many publications [4-9]. The level of vibrations, according to EN 60745, is estimated for the drill bit diameter of 8 mm and for pressure between 120-180 N. Yet, in these sources [4-9] different drill bit diameters are not mentioned. It is hypothesized that there is a rising linear relationship between vibrations measured at the handle of a tool and the tool’s working diameter. This data is vital because of the vibrations’ influence on health [10].
2. Measurements
As a part of the research a series of bore-holes were made in reinforced concrete girders (vibration-compacted concrete). During the tests a impact drill with pneumatic stroke: HITACHI DH 22 PH, and power 620 W was used. Declared by the manufacturer, estimated in accordance with EN 60745, the vector sum of weighted rms vibration acceleration values is 13.2 m/s2, which exceeds the permissible value of 11.2 m/s2 [2]. In the research two triple-axis vibration acceleration sensors DYTRAN 3023M2 cooperating with an 8-channel acquisition module VIBdaq 4.1 were used simultaneously.
During the measurements the front handle (regulated) of the device was oriented in such a fashion, that its axis was perpendicular to the corpus’ symmetry plane. During the tests a set of 9 widia single drill bits with an SDS-plus shank of a diameter from 6 to 22 mm was used. The measurement sequence began when the device was started. In the moment of startup the drill bit was touching the girder. The aim of this procedure was to enable the vibration level measurement also during the startup – in other words, during the transient state. The tests were conducted in a standing position, in the downward vertical drilling direction. In order to minimize the vibro-acoustic effect’s influence on the operator, a simultaneous measurement was conducted in three mutually perpendicular directions on both sides of the handle of the tool. To obtain representative results, a total number of 34 operators participated in the tests (12 women and 22 men), aged 22 to 26. Each of the participants made 18 holes, 2 for each drill bit.
3. Research results
During the tests rms vibration acceleration values were measured for three mutually perpendicular directions, for both the front and the rear handle, at the same time. Every operator held the device in such a way, that their left hand rested on the front handle and right hand on the rear handle. Spatial orientation of the measurement directions, related to a tool, is following:
– the direction (axis) corresponds to the longitudinal axis of the spindle of the drill (drilling direction)
– the direction (axis) corresponds to the longitudinal axis of the rear handle of the drill (a handle rigidly connected with the tool’s body)
– the direction (axis) is mutually perpendicular to the other two.
Fig. 1Values of the vector weighted vibration acceleration aRMS of the drill handle in relation to the drill bit diameter; vector sum and values in the main directions
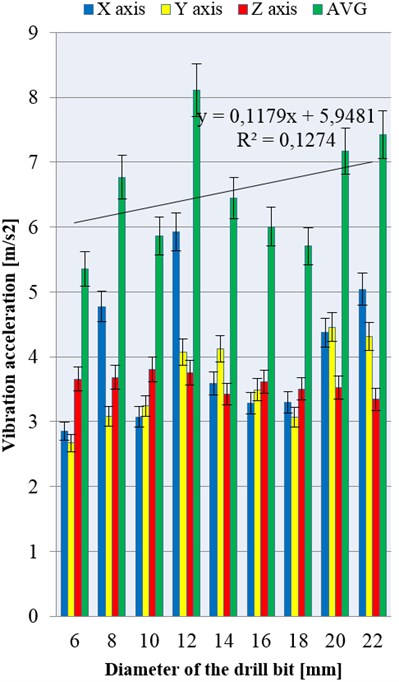
a) Front handle – left hand
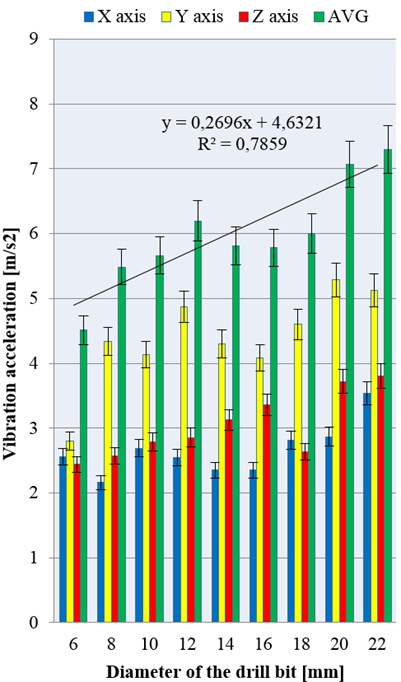
b) Rear handle – right hand
Fig. 1 illustrates the influence of changes of the working diameter size of a drill bit on the vector weighted total of vibration acceleration values. In case of the front handle we can state, that the linear correlation anticipated by the hypothesis does not occur. It is indicated by the determination coefficient because matching the linear model is faint. It can also be noticed, that the highest value of handle vibrations was measured for Ø12 mm drill bit, it was 8.11 m/s2. As for the rear handle, a growing dependency between an increase in vibration acceleration and an increase of the tool diameter was noted. This correlation has a linear character, which determination module equals 0.786; the degree of matching the linear model is satisfactory. The highest value of vibration acceleration was observed at Ø22 mm and it amounted to 7.43 m/s2.
By relating the values above to catalogue ones and comparing them to the data mentioned in [1] it can be stated, that the test tool belongs to 25 % of the drills available on the market which create the lowest amount of vibrations. The values of vibrations are 40 % below those declared by the manufacturer.
The influence of the tool diameter on the handles vibrations in the direction of the bore-hole axis ( axis) is not explicit and does not have unambiguously linear character, values of the determination coefficient for each handle do not exceed 0.6, which indicates a little matching the model. Similarly as in case of the direction, the correlation between vibration acceleration measured in the direction and the drill bit diameter is not exactly linear. The determination factor for the front handle is approximately 0.0534, which proves the lack of matching the model. In case of the rear handle the value is approximately 0.7, which is a satisfactory level of matching. But on the other hand, vibration value in the direction does not depend on the tool diameter. Admittedly, vibrations values rise, but the determination coefficient reaches values below 0.5 which translates into bad matching the model.
Table 1 presents the influence of changes of the drill bit diameter on the level of vibrations with regard to the direction and the operator’s sex. On the basis of the results it can be stated that women are more exposed to vibrations than men. This tendency concerns each of the respective directions and handles, as well as vector values. The only exception to the rule is direction of the front handle.
Table 1Vibration values with regard to the direction and sex for chosen drill bit values
Mean values (AVG) of vibrations accelerations for the respective directions [m/s2] | ||||||||||||
Drill bit working diameter Ø8 mm | Drill bit working diameter Ø18 mm | |||||||||||
Front handle – left hand | Rear handle – right hand | Front handle – left hand | Rear handle – right hand | |||||||||
Mean values | ||||||||||||
All operators | 4,08 | 3,41 | 4,78 | 4,27 | 3,30 | 2,43 | 3,76 | 3,83 | 4,09 | 4,62 | 3,46 | 3,43 |
Women | 3,93 | 3,58 | 5,50 | 4,20 | 3,93 | 2,84 | 3,98 | 4,59 | 4,87 | 4,82 | 3,47 | 3,78 |
Men | 4,17 | 3,31 | 4,38 | 4,31 | 2,96 | 2,20 | 3,63 | 3,41 | 3,67 | 4,50 | 3,45 | 3,24 |
4. Conclusions
Vibrations registered on handles of a impact drill depend on many factors:
– individual features and experience of an operator [4],
– position of a tool, type of conducted work and treated material [5],
– construction of the tool itself [6],
– construction and condition of the working part, bore- hole depth [7],
– frequency of the vibrations caused by tool and bit length [8],
– additional equipment fixed to a tool [9].
The tests partially confirm the hypothesis. A vector sum of vibrations measured on the rear handle of the drill shows a rising, linear dependence of moderate strength on the drill bit diameter. In case of the front handle such correlation was not noticed (see Fig. 1.). However, there is a possibility that the results were distorted by an influence of personal attributes and lack of experience of an operator. In order to eliminate this influence next research will be conducted on a maintenance-free device.
Information about factors influencing the growth of vibration level should be placed along with a declaration of such level by the manufacturer. Knowledge of such factors is vital not only for users, but also for constructors of tools of that kind and designers of personal safety products.
References
-
Griffin M. J., Howart H. V. C., Pitts M. P., Fischer S., Kaulbars U., Donati P. M., Bereton P. F. Guide to Good Practice on Hand-Arm Vibration. Non-Binding Guide to Good Practice with a View to Implementation of Directive 2002/44/EC on the Minimum Health and Safety Requirements Regarding the Exposure of Workers to the Risks Arising from Physical Agents (Vibrations), HAV Good Practice Guide V7.7. p. 12.
-
Skowroń J. Weryfikacja wartości NDN dla drgań mechanicznych o działaniu ogólnym i miejscowy (Verification of the NDN values for general and local mechanical vibration). Bezpieczeństwo Pracy Nauka i Praktyka (Occupational safety science and practice), Vol. 6, 2000, p. 22-23, (in Polish).
-
EN 60745-2-1:2010 Hand-held motor-operated electric tools. Safety. Particular requirements for drills and impact drills.
-
Neely G., Burström L., Johansson M. Subjective Responses to Hand-Arm Vibration: Implication for Frequency-Weighting and Gender Differences. Swedish National Institute for Working Life, 2001.
-
Shanks E. P., Hewitt S. M., Pitts P. M. Investigation of the relationship between vibration emission and in-use vibration for electrical tools, health and safety laboratory. Canadian Acoustics, Vol. 39, Issue 2, 2011, p. 104-105.
-
Oddo R., Loyau T., Boileau P., Champoux Y. Design of a suspend handle to attenuate rockdrill hand-arm vibration: model development and validation. Journal of Sound and Vibration, Vol. 275, 2004, p. 623-640.
-
Huang B., Kuang J., Yu P. Effect of crack on drilling vibration. Journal of Sound and Vibration, Vol. 322, 2009, p. 1100-1116.
-
Keith S., Brammer A. Rock-drill handle vibration: measurement and hazard assessment. Journal of Sound and Vibration, Vol. 174, Issue 4, 1994, p. 475-491.
-
Rempel D., Star D., Barr A., Janowitz I. Overhead drilling: comparing three bases for aligning a drilling jig to vertical. Journal of Safety Research, Vol. 41, 2010, p. 247-251.
-
Bjӧring G., Johansson L., Hӓgg G. Surface pressure in the hand when holding a drilling machine under different drilling conditions. International Journal of Industrial Ergonomics, Vol. 29, 2002, p. 255-261.
About this article
This paper was financially supported in the year 2015 by research project 02/21/DSMK/3470.